Our process - How we work
We process orders for the Snaplock® seam system based on concise order information. Below is how we work with clients and our scope of works.
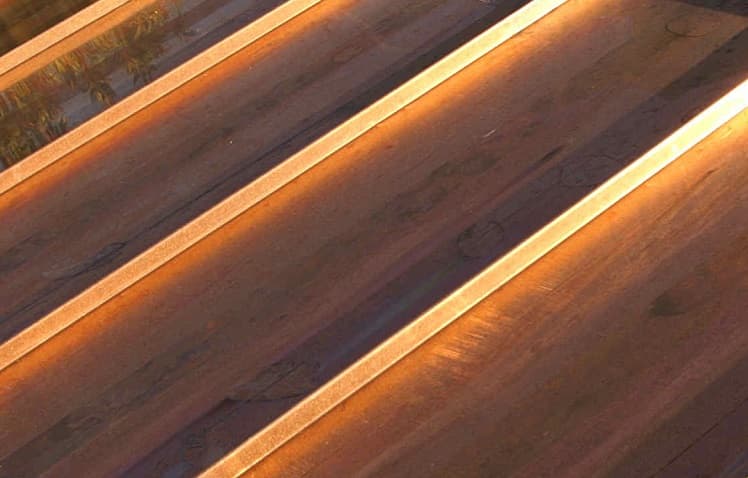
Discovering The Product
Snaplock® is a premium version of the snap-together standing seam panel system — featuring hidden fixings, high-quality metals, and strong warranty options. It’s widely chosen for both its appearance and technical performance.
Our role is to supply Snaplock® systems and related components based on clearly defined order details. We do not operate as consultants or estimators — customers must ensure they understand the system and what is required for their project.
We can assist during early-stage enquiries by offering provisional pricing based on defined components. However, accurate quotations always depend on receiving a clear, confirmed list of required items, lengths, quantities, and any relevant production drawings.
While basic drawings may help with initial estimates, all details must be checked and confirmed by the customer before an order is placed. It is the customer’s responsibility to understand what they need and to ensure the provided information is suitable for production.
Our pricing reflects both the size of the order and the amount of preparatory work required. The more complete and accurate your information, the faster we can quote — and the better the pricing is likely to be.
Below is a summary of the typical elements required for quotation:
Quotation Elements
- Type of metal & finish
- Panel type lengths and quantities
- Flashing types Lengths and quantities
- Related flashing production drawings
- Angle of roof pitch
- Cutting and folding tools
- Underlay
- Seam and flashing clips
- Nails and screws
- Sealants & touch up paint
- Rainwater Goods
- Roof light flashing kits
- Roof penetrations
- Tool Hire
- Training
- Delivery address & postcode

Finalising Order Details
Once a provisional quote has been reviewed and tentatively accepted, we move to finalise the order. This involves checking key dimensions, confirming any flashing drawings, and verifying quantities to ensure the order is production-ready.
If required, we will send physical metal samples to confirm the finish. Please note that while most samples arrive within a few days, delays may occur. Clients should notify us if samples are not received within one week.
Once the finish is confirmed and all order details are signed off, we issue a proforma invoice. Payment is accepted by bank transfer only.
Upon receipt of payment, your order is entered into the production queue and a provisional dispatch date is issued. This marks the start of the lead time and ensures timely fabrication and delivery.
If you're unsure where to start but have a live project requiring materials soon, it may be worth using our Provisional Schedule service. For £150 + VAT, we compile a detailed item list based on your drawings and project details. This helps establish what you'll need to order and ensures your quote is based on real components, not just m² estimates. If the project proceeds and an order is placed, this fee is fully refunded.
Clients are reminded that delivery does not include offloading facilities unless a Moffett is ordered at an additional cost. A suitable offloading area must be available on-site, whether for manual unloading or using a forklift if one is available.

Order Fulfilment
Once your order has been delivered, it's essential to check the goods immediately and report any damage to the driver before they leave. Photo evidence is required to process any damage claims.
If additional materials are needed later—due to under-ordering or site issues—they may be subject to standard lead times. That said, we always do our best to dispatch extras quickly to minimise disruption to your build.
Fortunately, the vast majority of deliveries arrive in perfect condition, thanks to careful packing and a detailed ordering process designed to avoid errors from the start.
We’re always happy to feature completed projects, so if you're proud of the result, feel free to share some photos—we may include them in our example gallery.
Key Takeaways
- Quality. Snaplock® combines premium materials with a hidden-fix design to deliver a sleek, architectural finish.
- Ordering Support. We can help prepare your order, but it's your responsibility to confirm the final list.
- Delivery. Orders are delivered to site for customer offloading. For additonal costs moffett offload can be arranged on request.
Product Over View - For the self builder?
Snaplock® is an ideal choice for simple projects. However, for more complex installations, some training is recommended.
While joining panels is easier than with traditional standing seam systems, it is important to note that not everything simply snaps together. Some cutting and folding of metal will always be required during installation. Although Merlin Metals does not provide training directly, we assist clients by clarifying key points and referring them to training if their project requires it.
Unlike other systems that secure flashings by driving fixings through the metal, Snaplock® is more closely related to traditional standing seam than industrial cladding. This means it avoids fixings penetrating the metal. Instead, flashings are folded to liner flashings, eliminating visible fixings and creating a more premium, seamless look.
- Eaves. This flashing goes into the gutter, the roof panels are folded around this to secure the eaves line.
- Verge. Panels may need cutting at the verge side and an upstand turning 90 degrees for the verge flashing to engage with.
- Ridge. The top of roof panel need folding up slightly and the ridge flashing requires folding to the ridge liner.
- Roof Lights. Custom roof light flashing kits require accurate planning.
- Wall Panels. Require a base flashing which the panels are folded around to secure the panels so no fixings through the metal are needed.
- Windows & Doors. Attention should be given to the layout and how the seams land so the correct flashings or panel folding can be planned.
Priority Schedules - Coming Soon
A new pricing strategy will soon be available for pre-qualified projects. Our Priority Schedules system allows selected customers to benefit from revised rates by aligning their order with our internal batch windows.
If your project is eligible, we'll let you know. This approach is ideal for jobs not requiring immediate fabrication and may offer significant savings.
Tell us about your project, mail@snaplockseam.co.uk
Mail Address
- Merlin Metals Limited
Unit 6 Malton Enterprise Park
6 Cherry Farm Close
Malton
North Yorkshire
YO17 6AD - Metal Samples Swatches
Available Upon Request